Cooling Tower Preventative Maintenance Plans | Cyrco, inc.
Cyrco, inc. Offers Annual and Bi-Annual Preventative Maintenance Plans: Clean, Lubricate, Calibrate, Repair, and Schedule Mechanical Replacements of Parts.
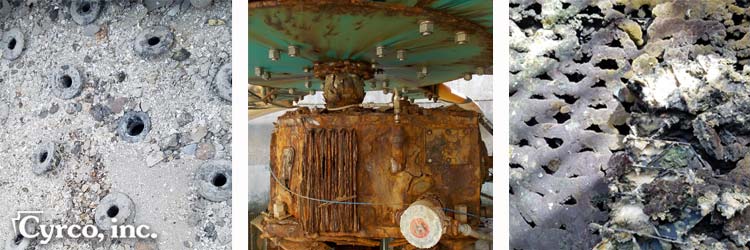
A regularly scheduled preventative maintenance plan equates to a more energy efficient cooling tower and reduces operational stress to mechanical parts which adds longevity to your cooling tower. In addition to maintaining optimized heat transfer rates, regular inspections and maintenance also notably diminishes equipment failure rates and unscheduled production shut downs. For our clients, production downtime is often unacceptable, represents lost revenue, and due to parts and personnel having to be expedited, a hefty emergency service repair bill. As with most mechanical equipment, it is generally wise to spend a little money up front in preventative maintenance for smooth operation and in order to save more in the long term.
Cyrco, inc. assists our clients with planning, budget forecasting, scheduling mechanical replacement, and implementing an annual or bi-annual preventative maintenance plan. Upon an extensive inspection of your cooling tower, Cyrco will provide a detailed, itemized proposal of a preventative maintenance plan that is custom tailored specifically for your cooling tower. We service all cooling towers including single or multi-celled factory assembled cooling towers, and field erected crossflow or counterflow cooling towers.
A list of preventative maintenance services that Cyrco offers, which may or may not be applicable to your cooling tower, includes:
- Drain cold water basin
- Remove sump screen to clean and inspect for damage
- Clean dirt and debris from cold water basin
- Check and tighten accessible cold water basin fasteners
- Clean hot water distribution basins to remove any solids obstructing spray nozzles (crossflow cooling towers)
- Replace any damaged or missing spray nozzles and verify all are properly seated (crossflow cooling towers)
- Mechanically wire brush and grind scale build up
- Remove drift eliminators and inspect for damage
- Inspect and clean water distribution pipes (counterflow cooling towers)
- Lightly pressure wash fill material while in place to remove any loose scale
- Pressure wash interior of tower to remove accumulated debris
- Pressure wash exterior of the tower and supports
- Lubricate fan shaft bearings
- Replace lubricant in speed reducer
- Lubricate motors in accordance with manufacturer's recommended specifications
- Inspect all couplings and drive shaft flexible elements for unusual wear or deterioration
- Verify proper mechanical alignments, adjusting as necessary to within +/-0.005"
- Check all fasteners within the plenum area for proper torque values to include inner fan cowling, fan stack, fan guard and mechanical components
- Check and tighten mechanical component fasteners and inspect for damage and wear
- Check belt and sheaves for damage and wear
- Confirm operation and setting of makeup water valve assembly-adjust as necessary
- Start-up the cooling tower and confirm proper operation
- Clean all debris from project
- Provide a detail report noting any deficiencies and recommended service
RELATED PRODUCTS: